|
 |
During the period from September 3 to 5, 2003, the 34th peer review was carried out at the Technologies Research Center, JGC Corporation (Higashiibaraki-gun, Ibaraki Prefecture). Over a period of two days in the peer review, Mr. Okubo, ex- Senior Associate Director of Sumitomo Chemical Co., Ltd., who is an expert on the chemical industry, participated as an observer from outside NSnet membership. We would like to introduce his opinions and impressions, which we have compiled below.
The purpose of introducing the observer on this occasion and the contents of the observer evaluation (perspectives) have been indicated separately.
|
1. Introduction

|
Thank you for letting me participate as an observer in the two-day peer review.
First of all, let me introduce myself.
I have been studying causes and counter-measures for chemical plant accidents and various problems at material user's sites for many years. In connection with nuclear power, I have also been engaged in solving corrosion problems in the reprocessing stage of the nuclear fuel cycle, which closely ties into the principles of chemical reactions.
I participated in this peer review from two standpoints. One is the standpoint of preventing and overcoming on-site accidents, which can be considered as a part of my career path. The other is from the standpoint of research center management, as the superintendent of the Technologies Research Center.
First, I will comment on the peer review from the standpoint of preventing on-site accidents. Then, I will comment on JGC's safety activities from the standpoint of the manager of a research center.
|
2. About the Peer Review

|
I was impressed when I saw that this activity is administered in a manner of a very high level of perfection. To comment on such an outstanding activity would be preaching to the choir. In view of my own experience in preventing accidents and disasters at production sites, however, I would like to comment on four points.
|
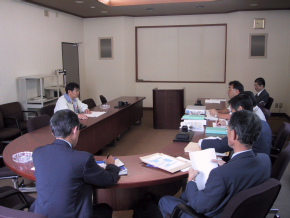
Observer confirming situation of an interview with the superintendent (front right)
|
|
1) Safety Activities
First, I would like you to notice that safety activities subjected to peer review are typical defensive activities.
Since old times, it has often been said, "Attacking is easy, but defending is difficult." This can be demonstrated by the case of the Iraq War. The advance onward and into Baghdad met with little resistance, but defending the prize after its capture and occupation is proving to be quite a challenge. This is self-evident. When attacking, you can concentrate all the force on the situation that is favorable. And under such circumstances of aggression, morale would also heighten. When defending, however, you must deploy your forces widely and thinly because you have no idea where the enemy will strike. And it is always your weakest spot that is attacked. In a defensive situation, it is not you, but the enemy who chooses the targets. You are always forced to take a passive stance. Under such circumstances, morale would suffer. Safety activities are exactly that kind of a job.
The most important thing in carrying out safety activities is knowing where your weak points are. As Sun-tzu said, "Know your enemy and yourself, and you will be ever-victorious." However, it is actually very difficult to know yourself. In peer review, I think it very important for you to brush up the review method, by which you identify the weak points of the target operation, and to build a mechanism that allows reviewees to become aware of them.
Although I will comment on JGC's safety activities in Section 3, I would like you to understand that even the brilliant achievement of running this Technologies Research Center without mishap ever since its establishment may become a weak point in terms of enthusiasm toward ensuring safety in the future.
On the contrary, we can see in the history of Du Pont an example in which it achieved a great leap forward by taking advantage of and reflecting on the negative legacies of accidents that occurred one after another.
One activity that is being carried out in the chemical industry, which includes top management, is the Responsible Care Activity. It is the placing of the basis of corporate managerial philosophy on coexistence and co-prosperity with society and by materializing various activities to achieve it as managerial policy. It was Du Pont that pioneered this proactive activity. Ironically, the history of Du Pont was plagued by terrible industrial accidents. The business of Du Pont, which started out as an explosives manufacturer in 1801, grew significantly with war demands in America in those days (e.g. wars with England, Mexico, and Spain, the conquest of the West, and the Civil War). However, explosive accidents always lurk in the shadows of explosives manufacturing. It is said that an explosive accident occurred every fourteen months even in peacetime, involving three deaths on average. Accidents occurred even more frequently in wartime when demand for explosives increased. During the Civil War (1861 through 1865), eleven explosive accidents occurred, in which 43 people were killed. During World War I (1914 through 1919), moreover, 347 people fell victim over a period of four years, partly due to the policy of committing numerous inexperienced workers and adopting the principle of production first. According to W. H. A. Carr in his chronology of the Du Pont Corporation, "It took a stomach of iron and nerves of steel to clear away after an explosive accident." By reflecting on these tragic accidents, Du Pont made a great change in its managerial policy from the principle of "production first" to that of "safety first." The managerial philosophy caring for society and employees in a broad perspective rather than adhering to immediate profits helped Du Pont ride out the great depression that hit the explosives industry after the end of the war by expanding its fields of business (e.g. converting explosives materials into automobile coatings). It also helped the business to grow and ultimately become today's leading comprehensive chemical company in the world, combined with its success in pioneering research and development of neoprene, nylon, Teflon, and more. It is a fine example of putting knowledge of weapons of attack to use in the promotion of safety (defense) efforts.
Although the activity called Responsive Care is in the spotlight today, I would also like you to take notice of Du Pont's course of history that gave birth to such a managerial philosophy rather than focusing attention on the result thereof. I would like to discuss the importance of history in the next comment as well.
|
Observer confirming situation of document examination (center)
|
|
2) Horizontal Dissemination of "Know-how"
The second point is about the horizontal dissemination of "know-how."
Although this is taken up as an activity subject to peer review, I would like you to take note that know-how works both ways; it may hurt you. There is a proverb saying, "A fool learns from experience while a wise man learns from history." Experience has an individual nature that is applicable only to the person or instance. It is necessary to dig into the experience if you want to disseminate and apply it widely and horizontally. A typical example can be seen in the criticality accident at JCO. Apart from legal regulations, the efficiency of on-site work had improved without criticality problems resulting from problematic operation. However, this know-how was merely experience with uranium having a low-level of enrichment, which did not apply to highly-enriched uranium. If they had delved into "know-why," the accident could have been prevented.
With regard to the Responsible Care Activity mentioned in the previous section, it is the history - the "know-why" that I would like you to learn, rather than simply copying the superficial - know-how. It can be said that history is information you will never get until you dig into events, bringing together causality and related factors as well as taking into account the lapse of time and the setting. It is not until you know the history (i.e. know-why) and your weak points that the precision of predicting the future (ensuring safety) improves. In peer review, I would like you to aim at the horizontal dissemination of good practices by scrutinizing the know-why aspects, rather than stopping at the stage of know-how.
3) Fate Surrounding Safety and Accident-Prevention Issues |
Observer confirming situation of field observation (back right)
|
|
The third point is about the fate surrounding safety and accident-prevention issues.
Although generally this problem could easily become a blind spot and it is not discussed very often, it is an important key to promoting safety and preventing accidents. Once accidents and problems occur, they come into the limelight and are forced to stand up against the storm of public criticism. However, if, owing to favorable measures and management, there are no problems, nobody pays attention, and it is simply taken for granted. This characteristic is easy to understand by comparing it to a baseball umpire. While umpires who make misjudgments are exposed to a rush of criticisms, good umpires are inconspicuous. This problem, which can be called fate, actually represents a significant issue that cannot be overlooked in terms of ensuring safety.
Let's look at an example of the problem of corrosion.
The corrosion of metallic materials begins when an ore that has existed stably in the natural world is processed into a naturally unstable metal by pouring a vast amount of energy into it. The reduced metallic material returns to the original ore (by rusting or oxidizing) in the natural course of things. The wisdom and technology of forestalling this natural course are included in the context of using the metal efficiently. However, people are not aware of the contributions from wisdom and technology because people take it for granted that metals do not corrode.
Here is an example of one particular chemical plant. At this plant which had a highly corrosive environment, expensive, high-grade materials that are superior in terms of corrosion resistance were required. Studies revealed that even inexpensive, ordinary stainless steel could be made to last by blowing air into it. The plant was constructed inexpensively by employing this technology. Fortunately or not, this air blowing also had the effect of preventing the product from being colored. Since ensuring product quality is a visible effect, the technology was steadily employed on-site. However, the corrosion-preventive effect became taken for granted and completely forgotten about after being used for many years without any problems. Later, energy saving became a major issue at this plant. It was planned to cut the power for blowing in the air. It was considered that discontinuing blowing in the air by using anti-polymerization agents would not affect product quality. However, the problem of corrosion that was the key to safety was overlooked because the actual record of no problems over many years had become a blind spot.
Safety technology has the fate that its contributions are difficult to be elicited. I hold out expectations that this peer review should work out ideas to shed light on the blind spots that people take for granted when no problems occur.
4) Measures to Further Activate Peer Review
Finally (fourth), I would like to express my personal opinion about measures to further activate peer review.
"You can lead a horse to water, but you can't make it drink." This American proverb is a warning that should be kept in mind when carrying out peer review activities. To encourage the act of drinking water requires a reward in which the act leads to gratification. An act without a reward is penance, but an act leading to gratification is not painful. For men, fortunately, a sense of achievement serves as a great reward. I would like you to make further efforts and work out ideas to elicit fruitful results, so that everyone participating in peer review activities can gain a sense of achievement. I understand that results of peer review activities have been followed up via questionnaire surveys for the members. The important thing is to elicit fruitful results in a form that is easy to understand for reviewees and third parties as well as giving reviewers a sense of achievement.
As an example, I would like to introduce the activities in the area of corrosion engineering. This area has an issue common to activities for safety in that it is difficult to elicit its results. I hope that this information will be of useful reference to you from that point of view. The Japan Society of Corrosion Engineering (JSCE) in conjunction with the Japan Association of Corrosion Control conducts surveys to determine the amount of economic losses caused by corrosion in Japan. So far, two surveys have been conducted, in 1975 and 1997, to clarify the actual status of corrosion in monetary terms that is easy to understand even for the public. In addition, JSCE studies to what extent corrosion could have been prevented with the application of readily available corrosion control technology, trying to elicit information about corrosion, effects of corrosion control technology, and the actual status of its application.
I expect peer review activities to work out ideas to dig up numeric results in forms that are easy for the public to understand, so that everyone can enjoy the results of the activities and a sense of achievement. Moreover, if problems concerning the activities to date can be identified through such analyses, improved activities bearing close to on-site activities can be expected by re-focusing on such problems to prevent upcoming second-round peer review activities from being stereotyped. What lies ahead of such a trend may be the goal of promoting and enrooting safety culture in the area of nuclear power.
|
3. Regarding JGC's Safety Activities

|
|
I would like to comment on JGC's safety activities from the viewpoint of having been engaged in the management of a research center. In the explanation of the management of the Research Center by the superintendent, I was very impressed that this Research Center has been operating without any accident for twenty years since its establishment. This is truly outstanding, which is the result of efforts made by each and every one of you, including leaders and researchers, following the resolution of the superintendent, not to mention his capability. In particular, as a matter of the superintendent's policy, I heard that safety operation is ensured by putting things thoroughly in order and being based on human relations in which everyone is familiar with everyone else. I was able to sense this from observing.
It is a significant achievement to attain a track record of zero accidents. In the real world, however, there are the bright side and the dark side. As you saw in the example of Du Pont, past accidents may serve as a strong driving force for future safety activities. It would be fortunate if the current favorable status of no accidents did not lead to a complacent attitude toward future safety activities. This may be one sign of such an attitude, but I did not see many safety signs or exhibits when I looked around the Research Center. This has the favorable side that it is not unsightly for visitors, but it is also worth considering that calls for safety should be repeated constantly. Since people have the habit of "running loose" if allowed to, I think you had better observe safety campaigns carried out by other operations as reference.
One extreme example may be the steel industry. When you go to a steelworks mill in the morning, you will hear workers greet each other with "Be safe" instead of "Good morning." This may have resulted from the lesson they learned from past accidents and disasters in the steel industry. In this sense, past accidents and disasters can serve as a driving force for promoting safety.
Twenty years after establishment, this may be an opportunity to stop and reconsider future actions. In this sense, I think it was fortunate to undergo NSnet's peer review here on this occasion, although I understand that you had to do a lot of advance preparations for it.
I pray that your favorable results to date will continue and further improve the safety and performance of the Research Center.
|
4. Conclusion

|
I would like to express my respect for the peer review methods you have established which contribute to improving safety and steadily accumulating fruits, and I pray for your further active involvement and prosperity.
|
5. Participation status of third-party observer (reference)

|
(1) Observer: Mr. Okubo
Position:
- |
Ex- Senior Associate Director, Process and Production Technology Center of Sumitomo Chemical Co.,Ltd. |
Main career and posts:
March 1954 : |
Graduated from the Department of Metallurgy, the Faculty of Engineering, Kyoto University |
April 1954 : |
Entered Sumitomo Chemical Co., Ltd. (assigned to the Research Department of Niihama Works)
Studied materials from the viewpoint of a chemical plant (materials user) |
|
- Selecting appropriate materials in new process development
- Developing corrosion-resistant materials
- Research into corrosion control
- Research into on-site accident analysis and corrosion prevention
- Research management in connection with production technology
- Others |
May 1969 : |
Research Associate |
March 1976 : |
Senior Research Associate |
March 1984 : |
Associate Director, Senior Research Associate |
March 1986 : |
Associate Director, Superintendent of the Engineering Research Center |
March 1991 : |
Senior Associate Director, Superintendent of the Process and Production Technology Center |
April 1994 : |
Senior Associate Director, but resigned as Superintendent of the Process and Production Technology Center |
February 1995 : |
Resigned as Senior Associate Director and became an Advisor |
February 1998 : |
Resigned as an Advisor and retired from the company |
Other external careers and posts:
- |
Guest lecturer of Niihama National College of Technology (in charge of metallic chemistry from 1970 to 1972, and modern chemistry from 1996 to 1997) |
- |
Director and Vice Chairman, Japan Society of Corrosion Engineering from 1989 to 1990 |
- |
Executive Committee Member for the 1994 Panel Discussion of Corrosion Engineering organized by JSCE, October 1994 |
- |
Deputy Manager of the Chugoku and Shikoku Chapter of JSCE from 1993 to 1996 |
- |
Advisor to the Chugoku and Shikoku Chapter of JSCE from 1997 |
- |
Honorary Member of JSCE from June 2000 |
- |
Director of the Chugoku and Shikoku Chapter of the Japan Institute of Metals |
- |
Member and Secretary of the Committee on Corrosion Engineering of the Society of Materials Science, Japan |
- |
Activities concerning corrosion issues at nuclear fuel reprocessing plants
- "Project Leader for the Demonstration Testing of the Corrosion-Resistant Safety of Reprocessing Facilities" entrusted by the Science and Technology Agency from 1980 to 1994
- Member of the Committee on the Evaluation of the Endurance of Spent Fuel Dissolver, Power Reactor and Nuclear Fuel Development Corporation (PNC) (currently Japan Nuclear Cycle Development Institute)
- Expert commentator for the Tokai Village Assembly regarding PNC's installation of Spent Fuel Dissolver
- Member of the Expert Committee on Reprocessing Plant Materials Technology, the Japan Atomic Energy Research Institute |
- |
Leader of the Inquiry Commission of the PCS (Petrochemical Co. of Singapore) LPG Refrigeration Tank Accident (Sumitomo Chemical/Shell, the Netherlands) |
- |
"Development of Nitric-Acid-Resistant Stainless Steel" received the Technology Award of the Society of Materials Science, Japan in 1988 |
- |
"Development of the Use of SN_1 Steel for the 'Storage and Transportation Equipment for Nitric-Acid Plants'" received the Japan Stainless Steel Association Prize in 1997 |
- |
Nuclear Safety Technical Adviser (Science and Technology Agency) from March 1998 to December 2000 |
- |
Expert Member of the Research Committee on the Safety of Nuclear Fuel Facilities, the Japan Atomic Energy Research Institute from April 1998 to until the Committee was disbanded |
- |
Member of the "Study Committee Concerning Commissioning Plans for Reprocessing Facilities," Nuclear Power Engineering Corporation (FY 2001) |
- |
Member of the "Subcommittee Concerning the Operation Control of Reprocessing Facilities from May 2001 to present |
Main writings and articles:
- |
"Stainless Steel Handbook (2nd and 3rd Editions), .Selection and Application, 1. Chemical Devices, 1.1 Chemicals and Chemical Fertilizer Industries" (The Nikkan Kogyo Shimbun Ltd.) |
- |
"Corrosion of Materials and Protection Against Corrosion" (Engineering Lecture Textbook for the Correspondence Courses organized by the Nikkan Kogyo Shimbun Ltd. and sponsored by the Chemical Engineering Association, the Nikkan Kogyo Shimbun Ltd.) |
- |
"Instances of Corrosion and the Latest Corrosion-Resistant Design and Construction Techniques, Comprehensive Collection of Materials, Chapter : Instances of Corrosion and Specific Countermeasures, Section 2: Instances of Corrosion and Countermeasures at Chemical Plants" (Management Development Center) |
- |
"A Dictionary of Rust Prevention, General Remarks, Anti-Corrosive Technology and Corrosion-Resistant Control Contributing to Extending the Life of Metallic Equipment, -5 Instances of Equipment Corrosion Control, - Points to notice in terms of protection against corrosion at acid manufacturing plants, - Points to notice in terms of protection against corrosion at alkali manufacturing plants (Industrial Research Center of Japan, Inc.) |
- |
"Materials Strength Science, Chapter 7, Section 3: Materials Strength and Design, Case Study, Tank" (the Society of Materials Science, Japan) |
- |
"Corrosion-Resistant Technology Handbook, .Actual Examples of Corrosion and Protection Against Corrosion, 6. Chemical Devices, 6.1 Chemicals (the Nikkan Kogyo Shimbun Ltd.) |
- |
"Modern Chemistry 2" (Fifth Year Textbook of Industrial Chemistry, Niihama National College of Technology) |
- |
"Corrosion Engineering Handbook, .Corrosion-Proof Testing, 1. Basics of Corrosion-Proof Testing Methods, 1.1 Purpose of Corrosion-Proof Testing and Points to Notice (Japan Corrosion Engineering Society) |
- |
"Pandect of Rust-Resistant and Corrosion-Resistant Technology, Chapter 3: Corrosive Function of Environments, Section 5: Acid, Alkali, and Salts" (Industrial Technology Service Center) |
- |
"Dogo Hot Spring and Ancient Romanticism" (Tourist Guide by Dogo Yamato-ya) |
And numerous other writings and articles.
(2) Peer review (location)
34th peer review (Technologies Research Center, JGC Corporation)
(3) Participation schedule
For two days, September 3 and 4, of the review term of September 3 to 5, 2003
|
|
|
|