|
 |
During the period from June 17 to 19, 2003, the 32nd peer review was carried out at the Takasago Equipment Plant (Takasago-city, Hyogo Prefecture), Kobe Steel, Ltd Over a period of two days in the peer review, Dr. Eng. Sayama, Professor Emeritus, Okayama University and Ambassador, Process Management Institute, participated as an observer from outside NSnet membership. We would like to introduce his opinions and impressions, which we have compiled below.
The purport of introducing the observer this time and the contents of the observer evaluation (perspectives) have been indicated separately.
|
1. Introduction

|
I worked at a company for three years after graduating university, after which I went back to university. I have been working safety measures at the complex in Mizushima since the heavy oil leak accident occurred in 1974. In the 30 years since, roughly 100 various incidents have occurred. Looking into the causes reveals one common element-the words "equipment failure". Put another way, a great deal of cases are when operation continues while ignoring dangerous breakdowns. In the end, the largest factor is equipment management. Therefore, I thought it would be faster to "eliminate breakdowns and problems" rather than focus on "eliminating accidents". Since then I've been involved in reliability engineering, safety, equipment management and safety management. I would like to present my opinions from the standpoint of those specialized fields.
Participating in this peer review has been extremely educational and I would like to thank everyone for being open.
|
2. About the Peer Review

|
I was surprised at the extremely vivid nature of the peer review materials. I thought "they've really taken a lot of trouble to produce this". I think a mutual exchange of opinions based on the raw data between the host (organization being reviewed) and reviewers is a very good idea. In that sense, I think the peer review is a very good system.
While opinions will vary quite a bit when looking at the nuclear industry or looking broadly at the machinery industry overall, I think peer reviews are useful in many ways from a broad standpoint for the machinery industry.
Review work is very difficult. While it may be easier if one is used to it, I think the load is quite heavy. However, I would by all means like to continue with the reviews in which one can learn a great deal in these reviews. They are particularly valuable if the content is fully used and acted upon in a steadfast manner.
For example in the High Pressure Gas Safety Institute in Japan, it is relatively difficult for people in companies to work on authorization, so people in all of the universities handle it. Naturally in that sense, one good way would be for reviews to be composed of people from various groups, such as companies and schools.
|
3. Equipment Management

|
ISO 9001 quality control is extremely good and putting equipment management aside, the concept of trying to improve quality is very strong. Equipment management is really the "source of occurrence". The equipment rattles around, making it very unstable, and once it's unstable, people get hurt when they try to fix it. Once a problem occurs, it has to be followed up and becomes a post-safety issue. Preventive maintenance generally can't be done. Since preventive maintenance isn't done, more breakdowns occur, becoming worse. When that happens, the plant is unstable, work increases and quality problems arise.
|
4. Visible Safety Control and Education

|
Having many patrols is a bad idea. The people at the site will think, "again?" and get stuck in routine. In particular, it is good for the managers to do it on site, but really what is necessary is finding what the "source of the occurrence" is. For example, safety problems in conjunction with accidents will not have their "source of occurrence" reduced unless breakdowns are reduced. Various problems must be looked by eye. This is done more easily if video or digital pictures have been made.
One way is deciding on various model work sites such as crane work and processing and videotaping that work site for all work done there, then evaluating the progress of improvements. In this way, one will see company-wide improvements if done well. Unless you videotape the site and show everyone what should be improved, they won't understand what exactly they are doing. Furthermore, these days, young people are not receiving enough education, and I would also recommend that they use the videos thoroughly.
While technical training for people on site is good, at the same time, people must be instructed in the ability to make improvements themselves. Therefore, it is not a matter of only "Disclosing 'hiyari-hatto' (near accidents)". What must be taught is "remembering the circumstances of near accidents and make them happen in this way". And not just looking at them in some obscure way, but draw out the near accidents with key phrases of "search for the sharp points" and "search for the wedged points". Also, create model equipment for the crane and have everyone look at a video and draw out the near accidents.
I would like to see efforts made to think of various ways to have people look at something with their own eyes in a way that is easier, faster and safer.
|
5. Conclusion

|
I made observations for two days. I think the intrinsic skills possessed by Kobe Steel are of an extremely high level. Put another way, based on the top technology in Japan, the company is steadfast in their operations. In that sense the passing down and continuation of technology is on an extremely high level.
Overall, I saw that everyone was working very hard, but on the other hand, management positions where people do too much is difficult for the company, so I would very much like to see the strength of the site skillfully brought out.
|
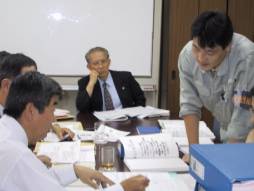
Observer confirming situation of document examination (center)
|
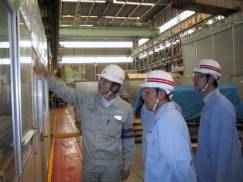
Observer confirming conditions of field observation (center front)
|
|
6. Participation status of third-party observer (reference)
|
(1) Observer: Dr. Eng. Sayama
Position:
- |
Ambassador, Process Management Institute |
Main career and posts:
- |
1958: Graduated Department of Chemical Engineering, Faculty of Engineering, Kyoto University. |
- |
1958-1961: Nuclear Power Division, Kansai Electric Power Company. |
- |
1961-1965: Assistant, Faculty of Engineering, Kyoto University. |
- |
1965: Associate Professor, Faculty of Engineering, Okayama University (lectures on equipment design controls, Department of Industrial and Mechanical Engineering). |
- |
1968: Doctor of Engineering. |
- |
1971: Professor, Faculty of Engineering, Okayama University. |
- |
1973-1974: Research Associate, Kansas State University. |
- |
1975-1997: Specialist, Loss Prevention and Safety Promotion Committee, Okayama Prefecture Complex. |
- |
1981: TPM Excellence Awards Committee Member. |
- |
1997: Retired from Okayama University. |
- |
Present Emeritus Professor of Okayama University.
Ambassador Process Management Institute. |
Publications:
- |
Plant Systems (Nikkan Kogyo Shimbun, 1972) |
- |
Chemical Plant Safety Measures (Maruzen, 1977) |
- |
FTA Safety Engineering (Nikkan Kogyo Shimbun, 1978) |
- |
Maintenance Handbook (JIPM, 1992) |
- |
Dictionary of TPM Equipment Control Terms (JIMP, 1994) |
- |
Advancing with Acceptable Worker Reductions at Plants (ed., JIPM, 1996) |
- |
Advancing with Worker Reductions at Plants, Vol. II (ed., JIPM, 1999) |
(2) Peer review (location)
32nd peer review (Takasago Equipment Plant, Kobe Steel, Ltd.)
(3) Participation schedule
For two days, June 17 and 18, of the review term of June 17 to 19, 2003
|
|
|
|