|
 |
The 119th Safety Caravan was held at Hitachi Zosen Corporation’s Ariake Works, on July 29, 2010. |
Safety Presentation |
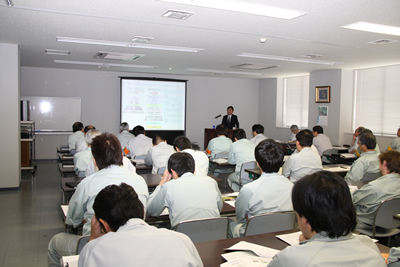
|
During the Safety Presentation
|
The safe practices presentation was attended by 35 employees of the Hitachi Zosen Corporation’s Ariake Works.
Prior to the main presentation, Takeshi Aboshi, General Manager Of Process Equipment & Nuclear Systems Unit Machinery Division, made a few opening remarks.
“We are extremely pleased to have members of the Japan Nuclear Technology Institute visiting the Ariake Works today, and we are greatly appreciative of the daily efforts that JANTI makes in ‘helping safety culture to take root and flourish’.
Here at the Ariake Works we manufacture nuclear power-related equipment, centering on casks and canisters, in accordance with our stated policy on quality, which is to ‘contribute to the safety of nuclear facilities by manufacturing and delivering safe and useful nuclear power equipment’.
This is the fourth Safety Caravan that we have hosted. I believe that the morning lecture and afternoon information exchange session will provide us with new ideas and strategies to apply to our safety activities and will afford us the perfect opportunities to further increase our safety knowledge and awareness. The main theme of today’s lecture and information exchange session will address a crucial issue for our plant as well as the manufacturing industry as a whole: human error. A single misstep through human error can result in major accidents and trouble. It is my hope that we will use Dr. Yoshimura’s lecture as well as the examples of best practices offered by Mr. Nobuyuki Onishi during this afternoon’s information exchange session as sources of ideas and strategies for eliminating human error and further invigorating our safety activities.”
Following the opening address, Dr. Seiichi Yoshimura Deputy Director, Human Factors Research Center Socio-economic Research Center Central Research Institute of Electric Power Industry, gave a presentation entitled “Lessons from Other Industries on Preventing Human Error – From the Perspective of Human Factors –”. |
Summary
of presentation |
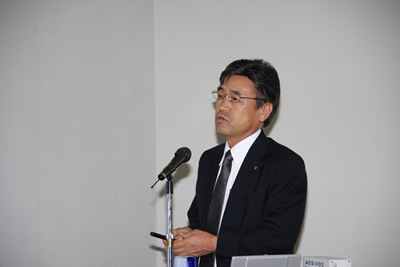
|
Dr.Seiichi Yoshimura
Deputy Director, Human Factors Research Center
Socio-economic Research Center
Central
Research Institute of Electric Power Industry
|
- Preventing the occurrence of trouble and accidents requires that we first understand the factors, i.e. the human factors, behind the human error that serves as the trigger for trouble and accidents; then we must put in place countermeasures and work to prevent recurrences. Also, it is important to have a “prevention perspective” which does not overlook even small events. In this regard there are a lot of lessons that we can draw from other companies and industries. It is important to be deeply engraved that, although the examples of industries are different from our own, they are still instructive.
- When we examine the causes of an accident, we need to identify the human errors involved, looking at the “people” and “operations and equipment/environment” involved during the “implementation phase” as well as the “planning preparation and assessment phases”; ultimately, we need to dig all the way down to the level of “daily management”. As a rule, when the underlying causes are clear, the countermeasures put in place to address them should not focus solely on the people involved; they should also focus on complementary areas, such as improving equipment and procedure manuals. It is also indispensable to check whether the countermeasures are carried out properly. Preparations of countermeasure must never forget to be is only the starting line for the prevention of recurrences to the last.
- Examples from one industry show a broad array of human attributes (such as confusion due to mistaken interpretations or misunderstandings, jumping to conclusions about or forgetting the lessons of past experience, relying on others (social loafing) and thinking only of that which is conducive to one’s own situation) contributing as background factors during the planning, preparation and implementation phases. At the same time, there were errors in procedure manuals that went unnoticed, requiring that some sort of safety barrier, such as “independent realization”, “realization through instruction by others” and “realization from some other source of information”, be in place at the individual level to promote paying attention.
In other examples, the common factors underlying repeated occurrences included lowered safety awareness and the devolution of safety measures into empty routines. To combat this, it is important to implement “know-why” education with regard to safety measures and to involve the all the members participation in the creation and revision of safety measures in order to prevent employees from feeling as if safety measures are just a burden foisted upon them. Also, at the individual level a professional attitude towards safety needs to be fostered, whereby the individual views themselves as the last and best defense against safety.
- In the examples of another industry, human characteristics that is going to take its ease is nominated for one of rear factors, but, as for this, it is it in the soil of the rule violations. The results of a survey on rule violations found that more than half of all respondents felt that “I obey the rules because those around me are obeying the rules.” Underlying this is the human propensity for social conformity, and by making skillful use of this, for the good practice, some workplaces were able to foster an atmosphere of adherence to the rules amongst everyone. Human characteristics need to be taken into account when considering operations and environments as well as the designing and implementation of safety measures in future.
- We can learn a variety of lessons from past examples, and it is my hope that you make use for prevention activity of the future human error while planning the horizontal development of a past example.
Some comments and response from the audience survey taken after the presentation:
- Thank you for an invaluable talk today. It provided me with insights which can be applied to future efforts in my company to prevent human error through the prevention of human factors and other series of factors influencing people’s behavior. It was also instructive to learn about people’s thinking with regard to rules, specifically that social conformity motivates 55% of people to follow the rules because the others around them are following the rules, and I hope to apply this in the promotion of future initiatives.
- Thanks to the inclusion of so many specific examples, I found this talk to be extremely easy to understand. An idea how we noticed an error from a viewpoint of the prevention of the trouble or how reminded us of an error was fresh for me.
- The extremely detailed analysis of human error, which is something I have paid little mind to in my day-to-day work, reminded me that the cause of a problem involves a variety of factors. For my future work, I think about how I prevent a fall and mannerism of the safety awareness and practice it.
- I learned a great many new things from attending today’s talk. The human being takes his/her ease by all means. As a result, the human being raises human error. I want to be careful to this lecture contents enough.
- This analysis of human error was distinctive in its premise of “humans” as entities which commit error. In essence, this suggests that the key to eliminating human error is to minimize “human” involvement. On the other hand, reliance on “machines” still presents us with issues of reliability. Thus, my understanding is that a balance of “human” and “machine” is important.
- This talk helped clarify the issue of human factors / human behavior patterns, something which I had only vaguely considered before now, and will be an instructive reference point for future efforts. Thank you.
- As for the accident and the trouble, I was able to understand that a problem of the human awareness happened in the main reason well , and that in order to reduce such problems, it is important to prevent negative chains of events from occurring by paying attention and not letting series of small errors go unheeded. I was also made aware of the fact that, because human memory is limited, it is important to prepare manuals.
|
Safety information exchange session |
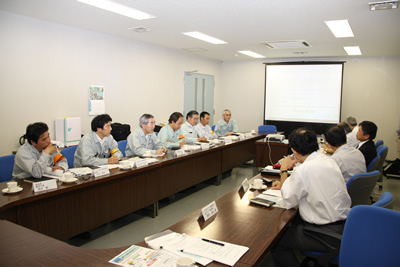
|
During the Safety information exchange session
|
During the Safety Information Exchange Session, Mr. Nobuyuki Onishi, Assistant Quality Assurance Group Leader at the Shikoku Electric Power Company’s Ikata Nuclear Power Station, gave a detailed presentation at the request of Hitachi Zosen on the “Human Error Prevention Initiatives of the Ikata Nuclear Power Station”. After the presentation, the participants exchanged comments and ideas regarding these initiatives. |
|
|