|
 |
The 118th Safety Caravan was held at Kobe Steel’s Natural Resources and Engineering Business Division in Kobe, Hyogo Prefecture, on June 25, 2010. |
Safety Presentation |
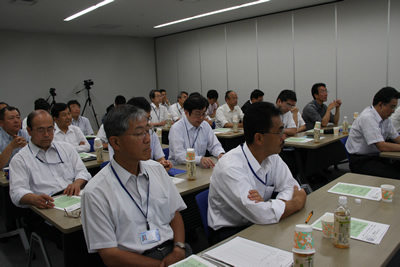
|
During the Safety Presentation
|
The safe practices presentation was attended by 30 Kobe Steel employees.
Prior to the main presentation, Keizo Yamamoto, general manager of the Nuclear Power & CWD Department of Kobe Steel’s Natural Resources and Engineering Business Division, made a few opening remarks.
“Today’s visit by NS Net and the Safety Caravan provides us with an opportunity to re-examine how we engage with and treat safety and its practice. All employees at Kobe Steel share the fundamental principle that the first priority of our business is always safety and quality. Nevertheless, our challenge is ensuring that this fundamental principle remains firmly entrenched throughout the entire organization. Our efforts in this area can be seen as resting on two pillars: ‘consciousness’ and ‘knowledge.’ Although we can appreciate the first of these, ‘consciousness,’ logically, our moods and emotions are susceptible to fluctuation and fatigue. Thus, how to stay emotionally connected is a key issue. We are currently devising a number of stimulation measures, including regular meetings and messages from senior management. The second pillar is ‘knowledge.’ When repeated incidents occur — like traffic accidents, for example — we naturally analyze the incidents to find out the nature of the problem: at what times and at what intersections are the accidents happening. Knowledge, then, is the process of scientifically analyzing past events to find a concrete solution to the problem at hand and steadily erecting safeguards and preventative measures. Thus, we aim to address safety issues whenever and wherever possible through both ‘consciousness’ and ‘knowledge.’ In this regard, I believe today’s presentation by Professor Inoue from Kanto Gakuin University will get you to think about safety from a new perspective. Thank you very much.”
Following the opening address, Professor Shiichiro Inoue, dean of Kanto Gakuin University Colleges of Human and Environmental Studies and senior researcher at the Institute for Science of Labour, gave a presentation entitled “What is the human error-tolerant organization?” |
Summary
of presentation |
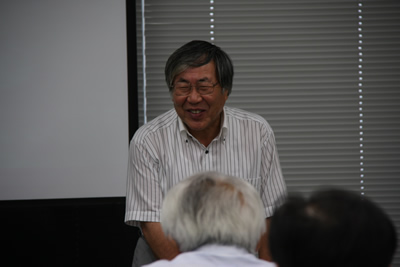
|
Professor Shiichiro Inoue
Dean of Kanto Gakuin University Colleges of Human and Environmental Studies
Senior Researcher at the Institute for Science of Labour
|
- Human factors came into being as a field of scholarship in the wake of the Tenerife airport disaster, in which two jumbo aircraft collided on a runway, killing 584 people. The accident was caused by human errors in communications between the two aircraft. Investigators found two underlying factors: the existence of a double standard between aviation law and pilot discretion and the occurrence of human-intrinsic errors compounded by demanding weather conditions. Like the Tenerife disaster, many accidents have happened in the past that were not caused by mechanical or system failure. Investigations and remedial measures for these accidents are often tackled within technical frameworks, but it is important to adopt concepts from human factors, which studies human behavior.
- Human behavior can be divided into several stages, such as perception, recognition, judgment, and attention. But in all stages, humans function under the influence of biological traits and do not simply absorb external information as it exists. In other words, when a person receives external information, he or she first attaches significance to the physical stimulus and then processes the information before the information actually has meaning. We must understand, then, that the potential for human error resides in this process of attaching significance to external stimulus.
- Human errors consist of unintentional acts and intentional acts. Strategies to counter human errors will not be successful unless they first clearly come to grips with the type of act they are dealing with. Because human error is a result, not a cause , it is important to remove and eliminate factors that incite human errors. Ever since the Chernobyl disaster, organizations have been told that what they need is a safety culture. And while safety culture has reached a critical mass of penetration in recent years, it remains imperative to keep safety culture and its practice from atrophying.
- The state of the organization around them deeply impacts humans in their workplace. If organizational factors are tightly managed, fluctuations on the personnel side can be contained at the near-miss stage and not reach the incident stage. On the other hand, if an organization is loosely managed, the occasional miss on the personnel side can suddenly develop into a full-blown accident. Controls that manage the easier aspects are generally more effective against human errors than controls that focus on the complex mechanisms of human information processing. Safety culture is nothing less than the common recognition that deviations in human behavior are inevitable and the shared understanding among all employees that solutions should be devised on this premise.
Some comments and response from the audience survey taken after the presentation:
- I found the speaker’s point useful that more effective human-error prevention measures can be arrived at by deliberately not giving individuals choices in their training.
- The presentation gave me some new perspectives. The observation that human error is a result, not a cause, and the notions that we must eliminate the principle causes behind human error and that an organization can tolerate human error were very pertinent.
- Until now, I had only a vague notion of “human error,” but thanks to this presentation, I now recognize the importance of investigating the causes of human error and systematically eradicating them.
|
Safety information exchange session |

|
During the Safety information exchange session
|
Katsuya Nakamoto, manager of Kobe Steel’s Quality Assurance Office in the Natural Resources and Engineering Business Division’s Safety, Quality, and Environmental Management Department, gave a presentation on “Engineering case studies and efforts against non-conformance.” Jun Hamada, from of the Japan Nuclear Technology Institute’s Nuclear Safety Network Division, gave a presentation on “Safety culture and human errors.” After the presentations, the participants exchanged comments and ideas on these and other topics. |
|
|