|
 |
The 116th Safety Caravan was held at the headquarters of Nuclear Fuel Transport Co., Ltd. in Tokyo’s Minato ward on February 8, 2010. |
Safety Presentation |
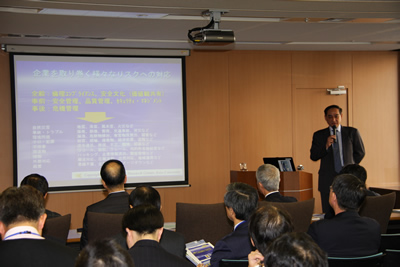
|
During the Safety Presentation
|
About 50 Nuclear Fuel Transport Company employees attended the session.
Mr. Yoshimitsu Kajii, president of Nuclear Fuel Transport Company, gave the opening address prior to the safety lecture.
“Today, we welcome the 116th Safety Caravan. Looking back at the records, I noted that our Rokkasho Transport Operations Office shared the honor, along with Japan Nuclear Fuel Limited, of participating in the very first Safety Caravan 10 years ago. This will be our fourth Safety Caravan, as we participated in the 60th and 89th Caravans too. In addition to these Safety Caravan, we have undergone two peer reviews by JANTI officials, who provided valuable guidance and advice. The aim of all of these activities has been to gradually and continually enhance our safety culture. Our transport safety record of no accidents or disasters to date is a testament to all our employees’ dedication to enacting the salutary guidance these experts have given us.
“We invited Professor Kenichi Takano from Keio University to join us today, who will give a lecture titled ‘Organizational Management and Human Factors.’ Professor Takano is well acquainted with the circumstances in the electric power industry, having been active at the Central Research Institute of Electric Power Industry (CRIEPI) for many years.
“Human factors has become a popular buzzword of late, but it remains a very difficult issue — there is no completion point no matter how hard you work; instead, human factors is an issue that must continually be engaged and grappled with. It is no exaggeration to say that most accidents and incidents in our world today are caused by human factors. A recent example is the failure to attach pantograph bolts, an elementary human factors error, that led to problems with JR bullet trains, which had boasted an outstanding safety record.
“Speaking of forgetting to tighten bolts, we have also detected past non-conformities that originated with failing to tighten bolts concerning shipping containers of low-level radioactive waste. In the afternoon session, we will introduce our corrective measures in response to this incident and get recommendations and feedback from our guests, which we are also looking forward to.
“Please give Professor Kenichi Takano your full attention, as I’m sure you will find valuable suggestions for safety-first management.”
Following the opening address, Professor Kenichi Takano from Keio University’s Graduate School gave a lecture entitled “Organizational Management and Human Factors.”
|
Summary
of presentation |
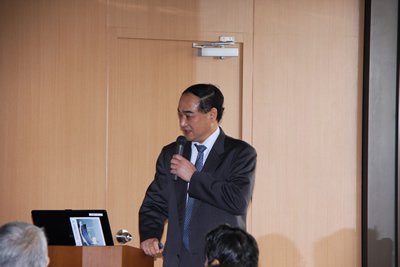
|
Professor Kenichi Takano Keio University’s Graduate School
|
- The presentation made the following salient points:
The environments corporations face have grown increasingly complex in the last few years, and the risks surrounding them are more diverse and farther ranging than ever. Given this situation, it is almost impossible to cover all potential risks with procedural manuals and organizational structures and policies alone. Therefore, what corporations need today is safety culture — that is, a shared a set of values. If members of a corporation can share values with respect to what should be prioritized, then the corporation should be capable of appropriately responding to any risk.
- Generally speaking, if an organization’s equipment operates smoothly, there will be no safety problems. But what supports this equipment is technology, and what supports technology is management. As long as management’s effectiveness remains static, problems will emerge with equipment operation regardless of how superior the technology is. Management, however, is intrinsically people-driven, and we should take the view that the largest problems lie within the organizational climate and culture, which shape management approaches. Consequently, the basis of safety culture is rebuilding an organization from the foundation by strengthening factors such as motivation, morale, and interpersonal relations.
- Some commonalities seen in Japanese industrial accidents are a deference to schedules and a sense of duty not to cause the company any harm. If we can deftly ameliorate these kinds of personnel and organizational problems, I believe we can prevent many more organizational accidents.
- At CRIEPI, we maintain there are eight factors essential to fostering safety culture. These are, to all intents and purposes, the same as JANTI’s seven safety culture principles. The first four — governance, commitment, communication, and motivation — form the underlying basis of the organizational culture. Governance requires efforts to instill shared safety values; commitment requires that the responsible officials have an awareness and recognition of safety; communication requires dialog with the workplace; and motivation requires the creation of mechanisms that incentivize safe practices.
- The remaining four factors — awareness, learning, enforcement, and resource management — form the basis of operational management. Awareness requires the persistent discovery and management of risks; learning requires thorough investigations of root causes and enhanced training; enforcement requires flawless verification systems; and resource management requires optimal personnel allocation.
- It is important to take these eight factors and build accident-prevention strategies using a five-tiered model — organizational responses, work operation preparations, acknowledgement and decision processes, actions, and equipment. It is critical, in view of sharing values, to find mechanisms that motivate workers to pursue safety on their own accord instead of activities that workers find forced or oppressive.
Some comments and response from the audience survey taken after the presentation:
- The presentation reminded me of the importance of efforts to sort out and prepare for potential risks. Many of the examples given in the presentation exploring the potential risk factors at other companies and highlighting declines and abnormalities are applicable to our workplace. It was a very useful presentation.
- The professor gave many wide-ranging examples of specific barriers to accident prevention. These will serve as good references when studying our safety management in the future.
- This presentation taught me that safety culture is intimately connected with corporate issues such as corporate ethics, risk management, and internal controls. I will try to apply the many examples presented here in my own work.
- I gained an understanding that analytic safety measure approaches are researched systematically based on specific cases. I believe many of these measures can be applied at our company. I learned that people’s psychological makeup is tied to shared decisions.
- From this presentation, I learned that problems and incidents arising from human factors cause enormous losses for corporations and that it is not only insufficient rules that cause these problems but that low motivation among all employees is a large factor as well.
- It was very worthwhile to hear a wide-ranging discussion, and particularly the causes of major accidents. The presentation also helped me better understand the shared values concept. From the practical pointers the lecturer gave, I sensed just how difficult it is to maintain safety.
|
Safety information exchange session |
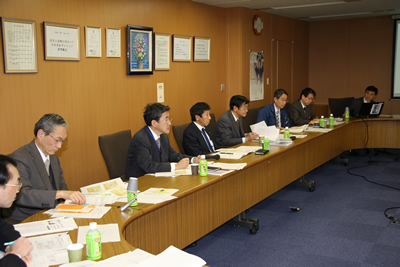
|
During the Safety information exchange session
|
Tadashi Inoue, manager of Nuclear Fuel Transport Company’s Safety and Quality Assurance Department, gave a detailed presentation on “Measures to prevent the reoccurrence of non-conformities with low-level radiation waste shipping containers and future lessons.” Six members of related departments, including Kazuhiro Suzuki, Nuclear Fuel Transport Company’s managing director, held a dialogue session from the perspective of “organizational management and human factors” on the examples and comments provided by Professor Kenichi Takano. |
|
|