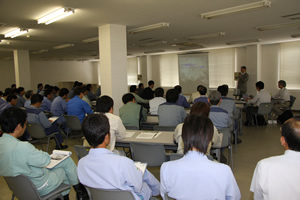
|
During the Safety Presentation
|
Approximately 65 employees of Kansai Electric Power Company's Mihama Nuclear Power Station and contractor companies attended the Safety Presentation.
The presentation began with an opening salutation from Mr. Hideo Kataoka, General Manager of the Mihama Nuclear power station.
"The outage of Mihama Power Station's Unit 2 due to troubles that occurred there which lasted for more than a year was completed on the July 30th, and thus we were able to have all three units in operation before the summer peak demand. We are grateful to all KEPCO and contractors personnel for their sincere maintenance management efforts that made this possible.
On the other hand, recently there have been many troubles and industrial accidents at all three of KEPCO's power stations that can be attributed to human errors, and we keenly recognize the need to promote safety culture and the preservation of safety to an even greater extent.
In a few minutes, we will be hearing a lecture from Mr. Kobori of the Maintenance Division of All Nippon Airways. The aviation industry, likewise to the nuclear power industry, feels a great deal of pressure and faces very strict demands concerning safety from the general public and safety regulations. They are also making very vigorous efforts in relation to the human factor, and even though it is a different type of industry, they share safety attitude in common with us in the nuclear power industry.
I hope all of you in attendance today will all devote your full attention to the lecture and take part in the various activities." After the opening salutation,Mr. Toshiaki Kobori, Deputy Director, Department of Quality Assurance Engineering & Maintenance and Senior Manager Planning %& Administration, All Nippon Airways presented a lecture entitled, "Human Factor Endeavors made by the Maintenance Division, All Nippon Airways -- Avoidance of Human Errors and Countermeasures and their Implementation." |
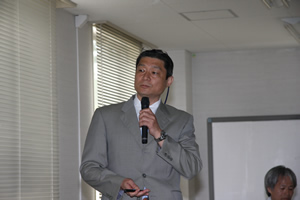
|
Mr. Toshiaki Kobori
Deputy Director
Department of Quality Assurance Engineering &
Maintenance and Senior Manager Planning %& Administration, All Nippon Airways
|
◆ Aircraft accidents caused by tangible hardware have been steadily declining as technology develops, but on the other hand, accidents due to human error have been on the rise. And accordingly, human factor related endeavors by the worldwide aviation industry have been in progress since around the 1980s.
At an aircraft maintenance facility, 80% of inspections are carried out visually, and in reality, it is impossible to eliminate human errors. In this kind of environment, we are continuing countermeasures on the concept of how to reduce human errors, and if/when errors do occur, how to prevent the error from being passed on to the subsequent processes.
◆ As one of the important endeavors in aircraft maintenance aimed at preserving airworthiness, ANA and other airlines create maintenance programs that take into account the circumstances that are particular to the company, and use maintenance programs of aircraft manufacturers as a reference. There are a wide variety of problems that occur during the course of maintenance, and we revise our proprietary program in response to these and information about the problem is also informed to the manufacturer and competent authorities, and when it is deemed necessary we receive feedback from the manufacturer, and strive for a higher level of safety based on the larger framework of PDCA that includes relevant organizations.
◆ As one of ANA's inherent characteristics of quality assurance, for most kinds of jobs except essential inspection items, we have adopted a system whereby each worker himself/herself confirms quality assurance by having each person inspect his/her own work (Self-Inspection). And so, through a system of worker certification, the Quality Assurance Division certifies the degree of skill of workers as a means of preserving quality, and in addition to assigning work in accordance with the skill level of the worker, the manual contains the QA bulletin drawn up by the Quality Assurance Division, and the Self Inspection Point is specified by making the worker understand in which part of the job the pitfalls lie. Furthermore, training is carried out using the "Basic Manners Handbook" which forms the basis of basic readiness and actions including such necessary elements as "tagging" and "pre-work briefings" which come before the manual. In addition to error control through endeavors such as these, we also implement error management using "ERA Analysis," which is a method of problem analysis that we developed in-house. Moreover, we make efforts to raise the skill levels of all workers through the use of human factors training.
◆ In 2007 it became obligatory for all companies in the aviation industry to adopt a safety management system and as a result, we have sought to make proactive endeavors in enhancing safety culture and adopting preventative measures through the use of near-miss information. I hope that by exchanging opinions with all of you here today who are engaged in the field of nuclear power which demands the same high degree of safety as the aviation industry, it will be beneficial in making further endeavors toward the human factor.
In the questionnaire after the presentation, the following opinions were expressed.
● The presentation was easy to understand and introduced factual conditions of maintenance in the department that actually adopted the system and the talk incorporated actual instances of failures that are not easily spoken about to people outside one's own company. The candid talk about the dilemma of the ANA Quality Department as to whether "following the manual is all that really matters for every job" gave the lecture affinity.
● From the lecture I understood quite well the efforts being made to thoroughly investigate the causes of past incidents with the aim of preventing recurrence as one of the human factor endeavors by ANA's Maintenance Division. Furthermore, accompanying the introduction of the safety management system, endeavors are being made to construct a framework of safety culture within ANA from the organizational level to the personal level, and information is being actively shared regarding the use of TAKO (NB: system for making use of near-miss incident reports) , anecdotes from the work places things noticed by each employee and problems, and it is my feeling that the endeavors to make even greater improvements from now on is the style which should be the model for all companies.
● The specific explanations about the actual state of maintenance on the frontline of the work-place were very informative. It reminded me that it is important to recognize not only tangible, but also the intangible endeavors including human factors.
● The lecture was very informative, as the demands made by regulations and society regarding maintenance work in the nuclear power industry and those regarding maintenance work in the aviation industry are similar. The lecture contained many useful points, like especially the reflections on trouble data and basic manners necessary for fundamental thoroughness.
● I understood quite well the details about endeavors toward HF that the ANA Maintenance Division is making. Troubling matters faced by our company also have many points in common and there are a number of points with which I can empathize, making this a very informative lecture. I also understood very clearly about the endeavors you are making to enhance safety culture activities, which is useful information.
● Through the introduction of examples of human errors, despite being a different industry, I was reminded of the common problems we both face concerning the human factor. I believe the TAKO endeavor is a very good concept.
● I was able to learn from the lecture about the state of ANA's quality management and human factors, and since I was able to see the common points and points that could be made use of in the power plant, it was a very significant lecture. |
At the request of Mihama Power Station of Kansai Electric Power Company, the safety information exchange session was honored by the presence of Mr. Takumitsu Sato, Staff Manager of the Nuclear Power Department, Kawasaki Factory, Power Generation Plant Business Office, Fuji Electric Systems Co., Ltd. who gave a detailed introduction of "Making Effective Use of Near-miss Incidents in the Manufacturing Division."
After the talk, information and opinions were exchanged regarding the above-mentioned endeavors.
|