|
 |
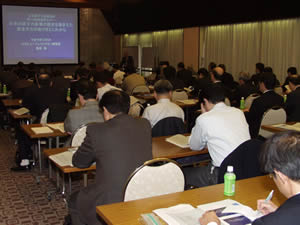
During the Presentation
|
The 14th Managers' Seminar was held at the Bukkyo Dendo Kyokai in Minato-ku, Tokyo on December 5, 2007 with approximately 50. manager-class personnel from member organizations in attendance.
Following the salutation by Executive Director Yasuro Suzuki, the seminar proceeded with a lecture that focused on the organizational factors, ethics, and the human factors that underlie safety culture and which are thought to be the root causes of the accidents, troubles, and improprieties that have come to light both within and without the nuclear industry, and members shared their awareness with each other. |
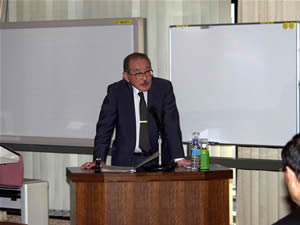
Mr.Isao Kuroda,
Director, Japan Institute of human Factor
|
Lectures
First Session
Lecture Title: "The Way Safety Culture Ought to Be, Based on the History of Japan's Nuclear Industry, and Hereafter,"
Mr.Isao Kuroda, Director, Japan Institute of human Factor
The word "safety" as it is used at nuclear power plants is used to express a variety of things, such as nuclear safety, safety of equipment, work safety, and the like. However, these forms of safety are subject to the whims of the IAEA, and one cannot help but feel that to the average person, safety is something different.
Recently, the western style large scale safety management systems such as QMS in the nuclear industry and SMS in the aviation industry are starting to be adopted in Japan. As the demands from the general public in regard to safety become increasingly more stringent these days, the pressure on the necessity to take a new look at the attitudes toward safety within Japanese organizations is growing. In the sixty years since the end of the war, Japanese organizations have built an outstanding proprietary framework for safety. However, there are trends toward emphasizing the placing of the blame and overly relying on administrative regulation instead of the prevention of recurrence, and numerous other tendencies that should be called demerits are seen. The concept of safety changes with the progression of time, and the structure itself should also change along with it. However, Japanese organizations are not well equipped for this in times of long-term recession. The current state is that familiarity with the western style structure has not been attained, and this gives rise to a myriad of scandals and troubles. Safety is defined as "danger that is judged as not exceeding the maximum permissible limit," but the question of where to draw the line as the maximum permissible limit is of the essence. First of all, we must bear in mind that safety is the methodology by which the organization achieves its objective, not the objective itself. If safety is to be the top priority, we need to also precisely clarify the order of priority of quality and schedule. That point is very fuzzy in the case of Japanese organizations, and this is one of the factors that poses problems for people at the actual work site. Also, we need to sufficiently understand that there is no such thing as safety that is completely independent from human intervention. As long as there are humans engaging in all sorts of tasks, absolute unconditional safety is inconceivable. Strong leadership is indispensable in order to promote safety culture, and it is the task of the management to create openness within the organization while directly participating in overall operations. In addition, other important elements are encouraging employees to think autonomously and act independently, accurate understanding of the human factors, and a lively organizational climate. Today, as society's awareness of safety continually changes, the roots of safety need to be reconsidered once again. It is important to continue making daily efforts as to how we can cultivate safety within our society. |
Second Session
Lecture Title: "Toward Restoration of Public Trust"
Mr.Hisao Shibue, Human Factor Group Manager, Quality Management Department, Quality Assurance Division, JAL International, Inc.
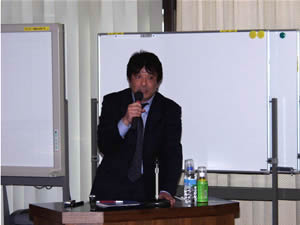
|
Mr.Hisao Shibue, Human Factor Group Manager, Quality Management Department, Quality Assurance Division,
JAL International, Inc.
|
The content of the lecture can be summarized as follows.
In the drive to recover the lost trust of the public, JAL has introduced a new safety management system (SMS). After receiving a directive to improve operations from the Ministry of Land, Infrastructure and Transport in March 2005, JAL launched a new project in the latter half of 2005 and a thorough investigation was made of the prevailing state of affairs. Based on those results, the Human Factor Group was established in April 2006, which is dedicated to human factors, as its name implies, and after four months of preparation the new structure was adopted in August of the same year. Attesting to the fruits of the endeavor, the number of human error cases in 2006 declined by nearly 20% as compared to the previous year, and the decline continued again in 2007.
The new system which makes use of "4M" was adopted in the field of aircraft maintenance with the major prerequisite being "providing our passengers with aircraft that they can fly in with peace of mind." The first M is for Man, and refers to the importance of individual skills; years of experience and training and qualifications. The second M stands for Method, and pertains to the manuals that are indispensable to aircraft maintenance, and while consideration of the manual itself goes without saying, the process by which manuals are created is also taken into account. The third M is for Materials, and relates to the management of parts and materials. And the last M is for Machine, the theme of which is the management of production of machines and equipment, and management of maintenance. In addition to the above 4 M's, we are also annexing two more M's, one being the question of what type of awareness program needs to be implemented for the staff of nearly 8,000 persons in order to achieve flawless Management, and the other is giving thought to our Mission of "why we have to perform maintenance on aircraft."
In order to manage these M's, JAL has employed the slogan "All working together, we shall completely eliminate the pitfalls!" and we are building a structure that incorporates the PDCA cycle. This PDCA cycle is based on seeking out the potential causes and implementation of basic measures, where there is a human factor advisor whom we call "Mr. Safety" who collects information and seeks out the hazards, and the MEDA program is put into effect to analyze causes and devise countermeasures, and then the measures thus implemented are scientifically evaluated.
Furthermore, the foundation for supporting this structure consists of a variety of activities such as a clear "top commitment" that adopts a "No Blame Culture" system whereby responsibility of the parties directly involved is not sought, a promotion system that includes the creation of a Network for advancing on-site leadership, and implementing thorough training programs in thinking for one's self. |
In the questionnaire after the seminar, the following opinions were expressed.
(1) In regard to the presentation by Mr.Isao Kuroda, Director, Japan Institute of human Factor
・I was keenly interested in the lecture about safety & economy and the movement of society. I have also been thinking about the way business enterprises ought to be hereafter. In the transition from the Japanese way to the International way, are the measures toward the change in the makeup of the structure (individuals, corporations, and society) valid? Or will administrative measures lead to individual happiness? What is an effective way for maintaining the balance between changes in national traits and demands of system changes? Next time there an opportunity to do so, I hope to hear the professor's thoughts on these questions. Thank you.
・In regard to the recent doubts and anxieties concerning "safety" mentioned, I felt very empathetic. As momentous changes take place, it is my desire to endeavor to place importance upon the fundamentals.
・As it was pointed out that safety has multiple meanings in the field of nuclear energy, I found myself in full agreement. In manufacturing, we tend to equate safety with safety of the workers, without having an awareness of overall safety. This lecture has caused me to change my way of thinking.
・The topics of "There is no such thing as safety, there is only danger. Safety is something created through the efforts of all individuals pulling together," "If safety is top priority, what is priority number two and number three?" and "We need to reconsider nuclear safety in Japan and return to the roots of safety culture" left a deep impression on me. I believe I have acquired a new thinking perspective for hereafter.
・ I found the lecture to be informative in regard to endeavors in safety culture, including my own conduct, by pointing out the nuclear industry's stance on "safety" from a broad perspective. Also, as to the question of the whether the nuclear industry is destined to decline if things continue on the current path, this has also been on my own mind for some time, and I felt the need to somehow hold this decline in check, and take pride in sending out a message to the general public.
(2) In regard to the presentation by Mr.Hisao Shibue, Human Factor Group Manager, Quality Management Department, Quality Assurance Division, JAL International, Inc.
・The 4M + 2M information is very useful. Being in charge of a work site myself, I hope to incorporate this as one criterion of techniques for management and maintenance of quality. I hope the "No Blame Culture" will catch on and become widespread throughout the nation. Despite bucking a headwind in some sense, I am looking forward to its adoption its adoption by your company.
・ The lecture introduced the actual state of creating a safety management system by the JAL Maintenance Division. I believe that the examples of making use of MEDA in the restoration of public trust should be most informative to the Electric Power Division if adopted for root analysis. I can feel JAL's enthusiasm.
・The human factor advisor is instantaneous, and I believe it is a good system.
・Hearing these actual reports is very informative from the perspective of restoring public trust after the occurrence of some trouble. I also learned information from the contents of the lecture that can be used in my own company's campaigns hereafter.
・The point of "creating a structure and creating the foundation that supports that structure" is that the structure should be kept within realistic expectations. Another point is that it must be a structure that functions normally. Drawing out the potential factors is also an important part of factor analysis. - And competence of the interviewer. Also important is grasping a perception of the true causes through repeatedly asking "Why?" And working out a No Blame Culture pointing out a clear policy as the top commitment. These points captured my interest.
|
|
|