A wealth of information was presented at the lecture, including the following:
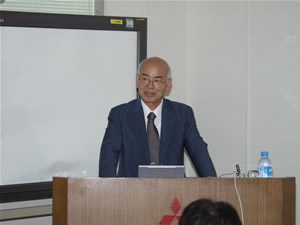
|
Doctor of Engineering Hiroshi Kai Director of Kai Safety Consulting Firm
|
1. Outbreak conditions of industrial accidents
In 2006 there were 1,472 deaths due to industrial accidents in Japan, 121,378 industrial accidents requiring at least four days absence from work, and a total of 550, 000 persons injured in industrial accidents altogether.
Analyses that categorize industrial accidents according to the types of conditions under which they occur, by scale of the work site, by type of accident, and by the origin of the accident go a long way toward clarifying the causes of why accidents and disasters occur, and are extremely important in order to educe and elucidate the most appropriate countermeasures for preventing similar calamities from recurring.
2. The causes of industrial accidents
Industrial accidents are when some injury-inflicting object comes into contact with a human worker, but the direct cause is that humans are responsible for unsafe practices and unsafe conditions such as the equipment, works, and work procedures. These are founded in "the four M's" (Man, Machine, Media, Management) which are consisted of deficiencies in safety management activities.Countermeasures against work-related deaths and injuries comprise grasping an accurate understanding of the unsafe practices and unsafe conditions, and establishing safety management measure activities built upon the principle causes of accidents.
3. Prevention of unsafe conditions
The source of most casualties resulting from unsafe conditions in the manufacturing sector is attributable to touching or getting too close to moving machinery. Preventative measures against these actions consist of training a sense of danger through risk assessment and establishing risk reduction measures.
4. Prevention of unsafe conditions
The source of casualties resulting from unsafe conditions in the manufacturing sector is largely attributable to defected work procedures and defects in protective measures and safety equipment. Preventative measures against these actions consist of establishing systematic safety management activities through an industrial safety and health management system that includes establishing work procedures, and safety measures consisting of essential safety design and safety protections based on equipment and machine risk assessment.
Comments from the questionnaires conducted after the presentation:
●I learned that in order to prevent industrial accidents, we had ought to prevent both unsafe practices and unsafe conditions. The lecture was very easy to understand. We are also endeavoring in risk management activities here in our company, but in reflecting upon the advice we were given during the question and answer session, I feel that we should make efforts to increase effectiveness from here on.
●Due to the characteristics of our business, I replaced the word "safety" with "quality" as I listened to the lecture. It was also informative from that perspective. We were presented with an abundance of convincing data.
●I understood quite well, and it taught me that when accident and disaster data are sorted into the proper perspective, it becomes extremely simple to explain in a straightforward way. At the same time, hereafter, although it feels only natural to give thought to preventative measures from a desktop point of view, costs and time are major influences in order to actually implement these at the worksite, so all in all, I have come to think that the industrial safety and health management system are also needed as a general framework.
●I am here from the Naka Research Center. Thank you for this lecture that will prove useful in raising the level of guaranteeing safety. The thing that left the greatest impression on me is the way of thinking toward dividing causes into direct immediate causes and fundamental causes, with the fundamental causes being categorized as the "four M's," and I hope these will serve as useful references in industrial safety and health activities hereafter.
●As a member of the Quality Assurance Department, as I listened, I applied everything being said to quality. It was a very informative session. All in all, I am troubled with the findings of the risk, and today's lecture has provided me with some hints.
●By starting off with the basic ways of thinking, then following up with specific examples and countermeasures and the like, the lecture was consistent and very easy to understand and will serve as a useful reference. In dealing with nuclear energy, safety is especially the top priority, and for this reason, today's lecture provides an excellent opportunity to rethink in specific terms about how to guarantee safety in places such as research laboratories which handle uranium and various types of equipment.
●Today's lecture was a reconfirmation that Man, Machine, Media, and Management factors have a major influence on safety activities. Of those four, it would seem that the human factor is probably the greatest. Accordingly, I believe it is important to create a friendly and strict environment for human. Realistically, however, I believe there are situations in which the time allotted for a job (process, submission deadline) is short, and it is not always possible to take sufficient measures, and it is not easy to deal with these situations. I believe the substance of today's lecture will be a useful reference in specific terms in our work.
●On the topic of making an international comparison of ways of thinking about safety, I was deeply intent on hearing about special characteristics that stem from national traits and the way these should be dealt with, and in addition to that, from here on into the future, I am deeply convinced that it will become a vital demand of society that this should be dealt with by selecting the ideal combination of the good points of each.
These and other opinions and impressions were expressed in the questionnaires.
Later, JANTI Director Hiroaki Kawashima introduced an overview of JANTI activities.
|