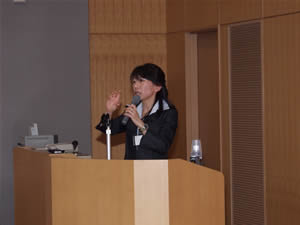
Ms. Yuki Shuto
|
1. Wednesday, May 30, 2007
(1) Lecture: Ms. Yuki Shuto, Chief of the Human Factors Division, Director & Senior Vice President of the Research Institute for Social Safety
Ms.Shuto gave a lecture entitled "What is True Safety Culture? Learning from Endeavors toward Zero Accidents and Case Studies of Past Accidents" touching upon the following topics.
An introduction was given summarizing the two accidents that brought safety culture into the limelight and how the Chernobyl accident led to the coining of the phrase "safety culture."
As far as safety culture is concerned, the idea of "making safety the foremost priority" is generally seen as clashing with the values of "economical, productive, and efficient." And because of this, to the people who actually work on-site at nuclear power plants, "safety on the job always comes first" and therefore they feel that "as giving priority to safety is a prerequisite, disregard for safety is unthinkable." And we tend to say that "it is only a very small number of especially deplorable companies that would throw safety to the wayside," and while the importance of "safety culture" is well understood, it is often the case that we are befuddled as to what it is that we should actually do in concrete terms. When we hear these voices from the workplace itself, the simple question of "are the values of economy and efficiency truly incompatible with those of safety?" must be asked. So then, when we make a detailed analysis of those examples of accidents in the past in which "safety culture within the organization" was the culprit, we see that the causes leading up to it are not necessarily a matter of making judgments in which "economic factors were put ahead of safety." Rather, the factor that caused the accident was the "normalization of deviance " whereby "workers gradually cease to obey the rules."
As a proposed method of making endeavors, examples of the unique endeavors that are actually being put into practice in the aviation industry and chemical industry were taken as the basis, and organized into the four steps of; (1) make "good rules", (2) make the rules widely and thoroughly known, (3) continuously monitor and confirm the state of compliance, and (4) evaluate the state of compliance and deal out rewards and admonishments as appropriate. |
2.Thursday, May 31, 2007
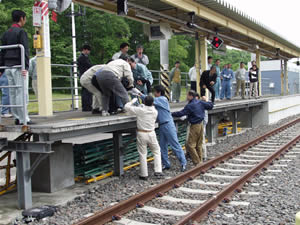
|
During the hands-on training
|
(1) Hands-on Training
JR East Personnel Service
Mr. Masao Sekiguchi, Advisor to the Training Department, HRD Division
The group acquired a wealth of on-the-scene hands-on training experience at the JR East General Training Center training line, such as training in dealing with emergencies within level railway crossings and training in the emergency stopping of trains in case of an accident at a level crossing and so on.
(2) Lecture: Mr. Masao Sekiguchi
Advisor to the Training Department, level crossing, JR East Personnel Service
Mr. Sekiguchi gave a lecture entitled "Reforming Safety Consciousness by Learning from Accident-causing Mistakes." In order to do the job safely, the lessons learned from the causes of railway accidents were sorted out from examples of accidents having to do with the foundation of the job and examples of accidents having to do with the foundation of safety, so that all attendees can take these back to their own respective work places and sound the alarm, as well as serving as a useful reference for creating a climate of safety hereafter. |
In the questionnaire after the seminar, the following opinions were expressed.
(1) About the lectures ・From the perspective of each business enterprise endeavoring in its own way to establish safety culture, and making efforts to eliminate on-the-job accidents, equipment failures, and the like, I feel that the explanation of the points based on examples from the past was valid. I believe that the examples brought up by Ms. Shuto in her lecture are significantly useful and that the lecture was easy to understand from every angle. Even though there are times when "obey the rules" conduct by major business enterprises often leads to failures due to differences in perception by each different individuals, I want to make efforts toward reducing such failures to the extent possible.
・I learned from the lecture that the problematic points are not that the rules are being broken, but rather, there are many rules that are difficult to understand or just plain unnecessary, rules that are difficult to obey, and rules written arbitrarily by people who know nothing about the job site. Furthermore, I learned that the true nature of the problem is that from the standpoint of safety culture, it is a serious problem, in fact an extremely serious problem, when deviation from the rules becomes the norm. Understanding of these matters is very useful to know.
・In both the Challenger accident and JCO accident there must have been countless processes (all avoidable) that lead up to those accidents. This being the case, why do accidents happen? Even though safety has not been ignored or disregarded, accidents still happen. Our hands are tied by the rules, and as a result of our hands being tied, we are left trapped in a catch-22 situation, and try to eliminate it. Such actions develop into human error and in the background of human error there are company management policies, and listening to today's lecture changed my thinking and renewed my awareness in many different ways. The lecture provided me with numerous hints regarding safety, which I greatly appreciate.
・The fact is, at the present time, there are too many rules and they are just too complicated. And there just is not enough manpower or time to reform the rules, forming a vicious circle. I will definitely try to think of ways to put the knowledge from today's lecture into practice.
・I came to understand the importance of top management's attitude toward safety, and rigidly adhering to the rules. The lecture left me with the feeling that it is important to fix those rules that cannot be obeyed.
(2) About the hands-on training
・Although it was hands-on training related to the railway industry, there are many things that the nuclear power industry has in common as far as endeavoring to prevent human error is concerned, making this a highly worthwhile training session. While there are countless concerns, such as confirming safety, issuing directives, carrying out duties accurately, appropriate information / communication / consultation, equipment & interlock remodeling and improvements and so on, I felt that it was important to train personnel, especially in raising awareness. I also recognized that management needs to have the ability to put these into practice.
・The safety endeavors made by JR East are extraordinary, and Mr. Sekiguchi's enthusiasm during his lecture really struck home the way it reached out into the audience, and in the hands-on training session, our endeavors were so earnest as to give us sore throats. I am very appreciative. The history of JR's accidents is a treasure trove, and I hope people everywhere are able to share in knowing it.
・I firmly understood that even if one possesses the theoretical knowledge, if there is an accident at the work site, appropriate response is impossible without conducting practice-runs on a regular basis. Being accustomed to doing something is more important than theoretical knowledge of it. I can feel the importance of forming habits as well as the importance of discussing matters amongst ourselves on a regular basis and hope to be able to pass this on to others in the course of doing my job.
・Although electric power is a different type of industry, the importance of safety culture and the basis of safety are the same, and preparedness is also the same. In dealing with emergencies at JR, such as rescuing a passenger who has fallen off the platform or whatever, it is only when one actually experiences this first hand that one begins to understand the basics of safety. Learning and experiencing this preparedness from the perspective of a supervisor has been an extremely useful experience.
・It was a most useful experience to have hands-on training while citing from the previous day's lectures. Rules are not obeyed simply because we are told to blindly obey the rules, but rather, one must consider the consequences of failure to obey the rules. I understood clearly that we need to bear the enthusiasm of having complete responsibility for the site. I am currently engaged in the duties of training, and I clearly understand that the instructor's enthusiasm has got to be felt by the trainees.
|