Lecture highlights
○For a business enterprise, safety is more than a simple matter of efforts toward preventing accidents (industrial safety), it is a matter of "carrying on business activities harmoniously and the state of attaining the planned objectives," and on this premise, "the requirements are to seek out the potential primary risk factors that impede business activities, and eliminate them, or limit them to within a scope that can be controlled." The idea that in order for a business enterprise to be able to carry on business activities without interruption, "it is important to judge the difficult relationship of balance between business activities and the countermeasures against primary risks factors, yielding business judgments that has to be decided by the enterprise's top management" was introduced. We heard in the lecture that safety, for a business enterprise, is precisely that "safety is tantamount to corporate profit," and quite simply, top management must ultimately take responsibility for it.
○Taking a look back upon the historical background of the term "human error," we sorted out its definition and way of thinking. Next, we differentiated between accidents and work-related deaths and injuries that are caused by systems as opposed to those caused by humans, and especially on the side of those caused by humans, human error and organizational mistakes were elaborated upon. Furthermore, in regard to the nature of errors, using behavior analysis train operation simulator experiments, he analyzed the process leading to errors for two types of human error: cases of accidents caused by a chain of mistakes, and cases of those based on failure to adhere to regulations.
○Workplace activation programs were introduced. They aim to activate the workplace through promoting communication within the workplace, and is a part of an effort to foment a climate of safety in the workplace. This program includes the two procedures of "seeing games" and small group discussions. It was explained that there was a high degree of reception to this program. The result of querying both the operators and management on their impressions after it was over revealed that "through communication, we were able to reflect upon the nature of our own behavior" and they felt "it was effective in accident prevention in a very interesting way."
○Lastly, two topics were covered. One was a case in which top management endeavored in safety activities by setting examples for all to follow. In this case, not only was there a reduction of work-related injuries or deaths, but also a reduction could be seen in product loss ratio, and in fact, production efficiency increased. It was concluded that safety is not merely a matter of accident prevention, and it is important to take the position that it facilitates production activity. The second topic discussed the "risk/cost" relationship dilemma which management is prone to fall into. In the early stages of corporate activity, the risks can be greatly reduced at a marginal expense, but as the business matures and the measures that need to be taken are already adopted, the risk is not reduced proportionately with the expense. He concluded by saying that as a result of this, management tends to lose the volition toward safety measures and focus on the profits in front of them. They are prone to falling into the trap of neglecting safety matters, and that is why it is crucial to pay close attention to this point.
After the presentation, the following comments were made.
•By rehashing the way we think about human error, it revived my awareness that education is needed to teach workers to think for themselves. I was also very much interested in the "seeing game" teaching materials as the methodology to approach this.
• Regardless of how much money business enterprises invest, safety risks will never be reduced to zero. But, I believe it is correct when it is said that if investment is stopped, accidents will increase. There is a trend for the people who design and manufacture the equipment and machinery we use to give top priority to profits, but we hope to carry out our work duties without forgetting to consider safety into balance.
•It was very interesting. Even though I have been aware all along of the top priority and utmost importance [of safety], this provided a good opportunity to think seriously about the vagueness of what we call "safety." From the perspective of what was said about the manuals just getting thicker as we adopt makeshift measures toward solutions when accidents and disasters happen, that is exactly the case. I believe that practical measures based on the presupposition that human error is bound to happen are what really count. This lecture takes perspectives that are slightly different from the usual ways of thinking, and these fresh ideas are very worthwhile.
|
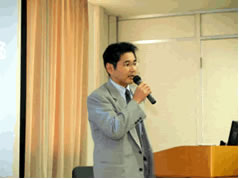
|
Mr. Nobuyasu Matsunaka
|
At the safety information exchange session, at the request of Kobe Steel, Ltd., we invited Mr. Nobuyasu Matsunaka, Manager
of Production Planning Dept,Machinery Factory, Machinery & Systems Hq,Mitsui Engineering & Shipbuilding Co., Ltd. Tamano Works to give a detailed explanation in regard to "improvement of and the passing down of skills through the preparation of 'skill reference lists'," which was extracted as a good practice at the Mitsui Engineering & Shipbuilding Co., Ltd. peer review.
The information and opinion exchange consisted mainly of the following: |
•What is being done to pass down technical skills? Also, if there are any other effective endeavors being carried out, please tell us about them.
•As for endeavors, in the case of welding, there is no alternative to OJT. The age structure is exactly the same as the age structure in our company, and we are aware of the issues. We are in the process of documenting the know-how that each welder possesses and creating a database.
• We would like to hear what you think about the way of creating corporate culture and safety culture.
• Basically, we think that all sorts of issues boil down to communication, transparency in the workplace, and pleasant working conditions. In the end, it is the top management of the plant that decides, but we want to move in the direction of where all persons in the plant have formed a consensus, and all personnel work toward accomplishing that goal. If we can succeed in creating such a climate and disposition in the plant, we cannot say that all of the problems pointed out will definitely be eliminated, but we believe the frequency of occurrence will be reduced.
|