|
 |
On 7th Sep.2005, the 75th Safety Caravan visited was held at ShimaneNuclearPower station,Chugoku Electric Power Co., Inc. located in Kashima-cho Matsue-shi Shimane Prefecture.
|
|
Safety Presentation |
About 105 persons, including the employees of Chugoku Electric Power Co., Ltd. and cooperating companies, attended the Safety Presentation.
At the beginning of the presentation, Shimane Nuclear Power Station, Chugoku Electric Power Co., Inc. station manager, Naoki Fukushima, made opening remarks stating, "right now, all around us,many different systems such as education, training, manuals,and procedures are being constructed so that 'mistakes will not be made' and 'mistakes will not be caused,'and it feels like we are apt to just be quiet and follow those systems. However, these are just illusions and what is really being asked of us is that we 'genuinely think for ourselves and take a course of action that is correct and put safety as the number one priority.' Today's lecture is entitled, 'Why do accidents occur? How developed countries are learning from their mistakes?' and I have been told that it is an introduction to examples of accidents overseas and dealing with safety. I hope that you will learn from it as if you experienced at yourself."
|
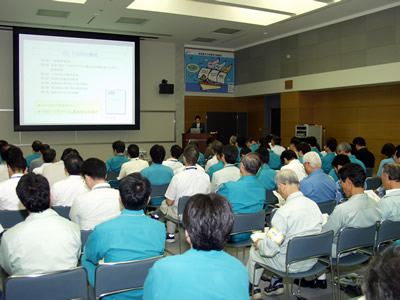
|
Safety Presentation
|
After the address,the Nuclear Safety Network (NS net) Division introduced the basic thinking and activity policies of the Japan Nuclear Technology Institute as well as the status of activities of NS net after which President of the Japan Functional Safety Laboratory, Mr. Ritsuo Yoshioka, gave a lecture entitled, "Why do accidents occur? How developed countries are learning from their mistakes." |
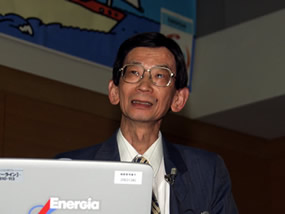
|
Mr. Yoshioka
|
During the lecture, root causes of an accident are and methods for analyzing such, as well as measures being implemented in developed countries were given.
-There are three root causes of an accident, 'a lack of safety culture', 'organizational structure problems', and, 'technology activity problems', the most important being, 'a lack of safety culture.' The largest cause within, 'a lack of safety culture' is 'overconfidence and self-satisfaction' in which there are seven categories, 'underestimating risk', 'relying too much on redundancy', 'nonrealistic risk evaluation', 'ignoring phenomenon that are severe but have a low potential of occurrence', 'assuming risk decreases as time goes on', 'underestimating software related risks', and 'ignoring early warnings signs.'
-The three causes of a serious accident are: human factors (competency), technical factors and organizational factors. These three factors are controlled by two goals that every organization has in common, in other words, economic efficiency and safety. Safety and economic efficiency can be thought of as the two axles of a car and they both need to be in balance.
-There is no such thing as zero risk or absolute safety. What is important is turning unacceptable risk into acceptable risk.
-In order to minimize the instance of error, it is necessary to recognize that humans do not set out planning to make mistakes, rather mistakes are a natural part of our actions.
-The design concept that risk can be reduced to acceptable levels if the safety-system that protects the safety of system functions correctly and operates is called 'functional safety.' This mechanism is based on the idea that 'absolute safety does not exist' and serves to relatively reduce risk through safety equipment and ensure a fixed level of safety through safety achieving functions.
-Safe products can only be born from a safe system. And, people are the ones who construct and operate that system. In other words, technical problems are not the only causes of accidents, the organization and the individual are fundamental causes as well.Therefore, if we do not regulate these things, safety cannot be protected. This is the basic behind functional safety standards.
|
Some comments on the questionnaire passed out after the speech noted, |
*Within the quality assurance activities based on the JEAC4111, in regards to nonconformity cause investigation (finding the root of the problem) which is a cornerstone of quality assurance activities, upon enhancing the nonconformity cause investigation related to human error I felt that the explanation of root causes"was very helpful. Thank you very much.
*I think safety relies not only on equipment but also on the health integrity of the individual and the organization. I plan to approach the safety and stable operation of a power station with a sense of mission and enthusiasm.
*People and organizations make safety and quality a reality, and atomic energy safety culture will not exist without these two things.
*I have an interest in this new word, 'functional safety.' We are often told about the importance of 'people' and 'organization' but the reality is that in the end what is evaluated is the product. I feel like importance is being put only on the proof of the system of quality assurance.
*The three causes of a serious accident are human, technical, and organizational. I understand that in regards to these three factors it is important to balance the two goals that every organization has in common (economic efficiency and safety), but I think that judging that balance is difficult and a source of concern. |
Safety information exchange session |
|
Safety information exchange session
|
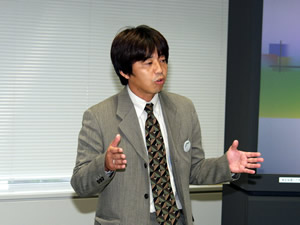
|
Mr. Hirasawa
|
At the safety information exchange session, in regards to 'Future Issues and Strategies in the Wake of the Mihama Unit 3 Secondary Piping Rupture Incident', assistant manager of the maintenance management department at Chugoku Electric Power Company's Shimane Nuclear Power Station, Mr.Shinji Nishimoto, gave a speech entitled, "The Fostering of a Safety Culture at Shimane Nuclear Power Station". In addition,assistant investigator from Tohoku Electric Power Company's Onagawa Nuclear Power Station, Mr.Akihiko Hirasawa, participated in the session and gave a speech entitled, "Introducing Information that Contributes to the Fostering of Nuclear Power Safety Culture." Mr. Hirasawa gave his opinions on communicating with cooperating companies and on the separation of responsibilities/system of cooperation with contractors as a lesson learned from the Mihama accident.
|
|
The main information and opinions exchanged included:
● |
In order to recognize and determine danger information in regards to such must be adequately conveyed to the top and it is important to make a decision after evaluating that information. |
● |
If you were to line all the plants up I think the corrosion tendencies would be obvious. But, of course different people inspect each site. Even if the number of units increases at the same site, the people who inspect them are different. I think this makes it easy for information to get 'lost in the shuffle.'In the case of Mihama, the communication gap between the cooperating companies and the electric company is focused on, but I think it's definitely possible that there were communication gaps within the electric company as well. It's easy for us to exchange information because we only have two units, but I think figuring out how to maintain a safe organization becomes more important as the number of units increases. |
● |
Just like in the 'test of conforming to the majority', I think it's hard to say that the person in charge of a certain area would think there is a problem if the majority of his/her managers/colleagues don't think there is a problem. If everyone from the top of the ladder to the bottom understands the importance of safety and the safety culture of the organization on a whole improvement , then the correct decision can be made. But, even that does not mean that there will not be accidents. That final decision may be mistaken. But, all we can do as mere humans is make decisions in a system where everyone on the ladder has safety awareness and culture. |
● |
One of the INPO's concepts is SCWE (Safety Conscious Work environment). This is the concept that, "having an environment in which one can freely express their opinions in regards to fears about safety without fear of punishment is important."We must have an environment where cooperating companies or electric company personnel feel that they can speak up if they notice something. It can also be said that we cannot construct a safety culture if this type of environment does not exist. |
|
|
|
|