|
 |
On 28 Feb 2005, the 72nd Safety Caravan visit was held at Shika Nuclear Power station, Hokuriku Electric Power Company, located in Hakui-gun Ishikawa Prefecture. |
|
Safety Presentation |
About 90 persons, including the employees of Hokuriku Electric Power Company and cooperating companies, attended the Safety Presentation.
At the beginning of the presentation, Mr. Shinji Wakamiya, Superintendent, Shika Nuclear Power Station, Hokuriku Electric Power Company, gave an address and said,
“Thank you for holding the Safety Caravan at Shika Nuclear Power station today. We are making efforts to accomplish a higher level of safety culture in the wake of last year's accident at Mihama Nuclear Power station. We will strive to prevent human errors and aim to improve our “safety culture” through insights gained from Mr. Yoshida's lecture. In addition, during the afternoon session he will introduce TPM activities, some good case studies from Hitachi Zosen Corporation. We believe that these activities are important for our plant and would like to refer to them in regards to future operations.”
|
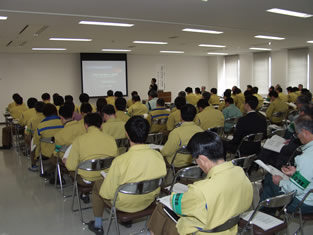
|
Safety Presentation
|
After the address, Mr. Machida, General Manager of NSnet, introduced NSnet activities, and this was followed by a lecture entitled “Organizational Safety Management and Understanding of Humanity-Group Dynamics of Human Error” delivered by Prof. Michio Yoshida, Center for Educational Research and Training, Faculty of Education, Kumamoto University |
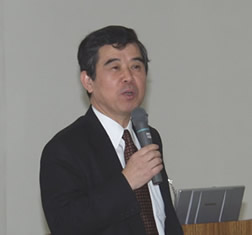
|
Mr.Yoshida
|
During the lecture He lectured on creation of safety culture in terms of organizational safety management and understanding of humanity.
-Design and operation of equipment and facilities must be fail-safe. An operator must feel unsafe. If he feels something wrong, he is required to consider it to be dangerous, being very sensitive to potentially danger events. He should not determine that it's all in his imagination and misunderstanding.
-If he has no “knowledge” on safety, he cannot ensure safety. However, even if he has the knowledge, an accident will occur. He is required to be “conscious” of making use of the “knowledge.” Furthermore, safety is not accomplished until his safety “awareness” leads to safety “action.”
-It is important for you to create an organization and corporate environment in which employees are willing to apologize for their mistakes. Without such corporate culture, near accidents, root causes of errors and accidents, do not come to surface.
. -There are five devil's rules that jeopardize an organization: “Habituation,” “Wrong generalization of experiences,” “Memory processing and story creation,” “No accident occurrence with manual violation,” “Accident occurrence even with manual adherence.”
-Organizational Peace/Health/Safety (PHS) cannot be realized until individual PHS is ensured. Moral is undermined before collapse of the moral. Moral-up greatly relies on the presence or absence of leadership. Human factor fundamentals are human relations and leadership.
-To eliminate human errors, it is desirable not to work. But, this does not serve as a problem-solving method. Serious accident risks resulting from human errors represent evidence of important works implemented. This is a real situation of a nuclear power station as an organization. In the sense, I want all of you to be engaged in your works with your confidence and pride.
|
Safety information exchange session |
|
Safety information exchange session
|
|
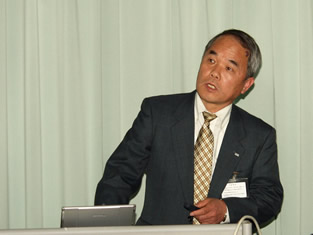
|
Mr.Yanagawa
|
At the safety information exchange session, we asked Mr. Hajime Yanagawa, the head of the TPM Promotion Office , Hitachi Zosen Diesel & Engineering Co., Ltd. , to give an in-depth explanation about the good practices cited by the peer review regarding “Implementation of Active Improvement Activities through TPM Activities.” |
The main information and opinions exchanged included:
● |
What types of educational activities are offered to your employees? |
● |
We hold an in-house presentation session on proposals for improved operations every two months and organize a presentation session in the area of Kushu twice a year that is joined by other industries. In addition, our inidividual work groups present their activities to our president twice a year. |
● |
Have these activities changed the morale of your employees? |
● |
Under the Part I Activity, the employees started to clean their workplace. Initially, they complained a lot about this cleaning, but some exclaimed after , “the plant looks clean” and “all the broken machinery and oil leaks are gone.” So, we belive that being able to witness these changes with their own eyes bolstered the morale o f the staff. |
|
|
|
|