|
 |
On 21 Jan 2005, the 69th Safety Caravan was held at the Yokohama World Operations Center, JGC Corporation.
|
|
Safety Presentation |
About 40 persons, including the employees of JGC Corporation and cooperating companies, attended the Safety Presentation.
At the beginning of the presentation, Mr. Kazunobu Inoue, Executive Officer, Senior General Manager, Research & Development Center, JGC Corporation, gave an address and said,
“We thank Mr. Hirakawa and all members of NSnet for organizing the Safety Caravan today in spite of being very busy. I think it necessary to provide opportunities to repeatedly consider and check safety in order to create a safety culture and ensure safety.Today's lecture and information exchange meeting are essential for not causing accidents, and assuring safety and then can be utilized for our future operations.”
|
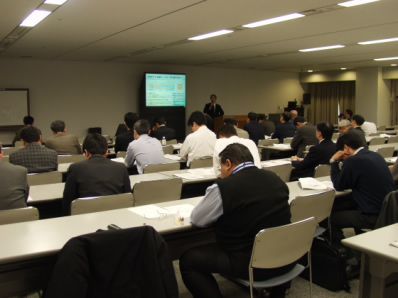
|
Safety Presentation
|
After the address, Mr. Machida, General Manager of NSnet, introduced NSnet activities, and this was followed by a lecture entitled “Safety Preservation-Hamaoka Nuclear Power Station's Approach to the Safety” delivered by Mr. Ichiro Hirakawa, General Manager of Nuclear Training Center, Hamaoka Nuclear Power Station, Chubu Electric Power Co., Ltd.
|
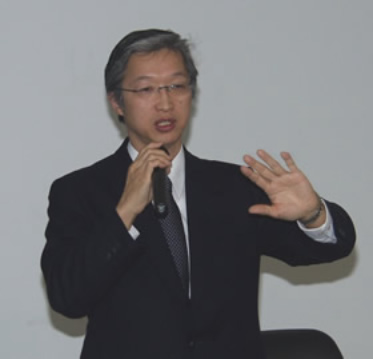
|
Mr. Hirakawa
|
During the lecture,
He presented lessons learned from several troubles that occurred at Hamaoka Nuclear Power Station, and cases in which safety operation has been addressed.
The “Gijutsu Densho Room for technology inheritance” was established at the Training Center within the station in order to maintain and improve technologies. This room, called “Corridor for Lessons Learned from Failure Cases”, is designed to ensure the conveyance of experiences learned from troubles occurred in the past (unsuccessful cases).
For increased management transparency, we provide information to local residents and the public via Internet and by station tours.
For shared information on non-conformances, a CAP meeting, an assembly for confirming maintenance information is held every morning. In this meeting, being joined by a plant manager, each division director, chief engineer, a top section chief and an on-site director at Hamaoka, who belongs to a management review office reporting to the President, information on non-conformances at a trouble indication stage prior to the occurrence of troubles are shared while a policy for measures against the troubles and response to them are confirmed as needed.
Our approach to safety conservation was introduced. We will continue to make efforts for aiming to be a reliable and safe nuclear power station. |

Safety information exchange session |
|
Safety information exchange session
|
|
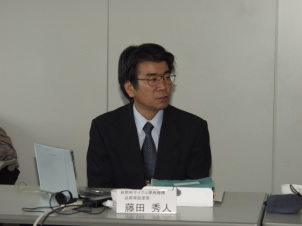
|
Mr. Fujita
|
At the safety information exchange session, Mr. Hideto Fujita, General Manager of Quality Assurance Section , Tokai Reprocessing Center, Tokai Works, Japan Nuclear Cycle Development Institute, gave a detailed presentation on “Improvement of Manuals and Improvement of Checking System for Preparation and Revision of the Manuals with involvement of Outside Experts”, a subject identified as a good practice in the Peer Review.
|
The main information and opinions exchanged included:
● |
When revising operation manuals and other documents submitted from manufacturers, various events into operation field would be reflected in the revision by the operator . If possible, we , manufacture wish to have an opportunity to receive feedbacks on reason for revision from the operator . For instance, if manufacturers can also learn experiences on past failures and errors through the “Corridor for Lessons Learned from Failure Cases” you mentioned , common safety awareness could be shared among manufacturers and suppliers, I believe. |
○ |
In the Tokai Works, I think it is not easy to send feedbacks on individual troubles directly to each manufacturers because many makers are involved in our operations. As a result, we have established a safety promotion council. Through the council, we want to introduce troubles, facility modification and revised manuals. |


|
|
|
|