|
 |
On 19 November 2003 , the 55th Safety Caravan visit was held at Nippon Nuclear Fuel Development Co., Ltd. , located in Higashi Ibaraki-gun, Ibaraki Prefecture.
|
Safety Presentation
|
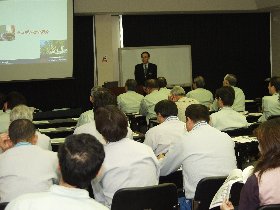
Safety Presentation
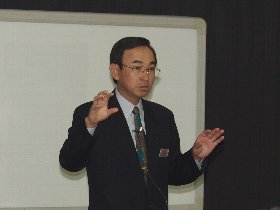
Ms. Takekawa
|
About 45 persons, including the employees of Nippon Nuclear Fuel Development Co., Ltd. and cooperating companies, attended the Safety Presentation.
At the beginning of the Presentation, Mr. Takemura, President, Nippon Nuclear Fuel Development Co., Ltd. , gave an address and said, "Fostering safety culture at our company is moving forward daily as we assimilate information from NSnet into our activities. At today's Safety Presentation, we hope to improve the safety consciousness of our employees and the company's efforts to improve safety by presenting good practices of safety as well as through the exchange of ideas and opinions."
After the address, Mr. Tanaka, General Manager of NSnet, introduced NSnet activities, and this was followed by a lecture entitled "Business Ethics at DuPont" delivered by Mr. Kunio Takekawa, Fulfillment Leader, Safety Resources, DuPont.
During the lecture he said, "Along with providing you with an overview of Dupont, I would like to present concrete specific information concerning the importance of business ethics, the policies and practices of business ethics, and the role of business ethics as a part of the corporate culture.
- |
Dupont's immutable core values include "a safe and healthy workplace," "respect for people," and "business ethics." |
- |
At Dupont, safety, respect for people, and business ethics are the responsibility of the top line management from the top. Furthermore, not only does the behavior of the top management set the standard for the company employees, it demonstrates the level of expectation. |
- |
At Dupont, business ethics applies to all business activities, and to all of those connected with the company's business activities. |
|
Safety information exchange session
|
At the safety information exchange session, we asked Mr. Takahara, Manager, Nuclear Power Plant Quality Assurance Dept., Pablic Utility Systems Group, Mitsubishi Electric Corporation. to give an in-depth explanation about the good practices cited by the peer review of the Energy & Industrial Systems Center, Mitsubishi Electric Co. regarding "prevention activity of human error at field erection site by the MAPLE (Manual Analysis Program for Lowering risk of human Error) Technique."
The main information and opinions exchanged were:
- |
With this technique, are there cases in which you offer feedback through something like a manual for design review, and do you conduct brushups when materials such as manuals, instruction documents, etc. identify danger factors? |
- |
This technique improves instruction documents. You can certainly improve materials such as instruction documents through post-job management of projects that take place year in and year out similar to regularly scheduled maintenance. However, the focus of this technique is to heighten the safety consciousness of workers at the completion of each project. |
- |
When extracting the factors determining the degree of risk, I believe those elements such as the evaluator's experience, subjectivity, etc. engender variances in the evaluations. I think that jobs in which the evaluation of dangers varies are more dangerous than jobs that everyone agrees are dangerous. How do you evaluate these variations? |
- |
That's right. When all of the workers on a project agree that it is dangerous, then the work proceeds carefully, and this helps to prevent human error and accidents. However, for jobs where the danger value is low, or for jobs where the danger value varies, those workers who feel the danger value is low are likely to make human errors. Therefore, it is the responsibility of management to analyze the causes, etc. of this variation with these types of jobs in order to prevent accidents. |
- |
I think that evaluating the differences in awareness among workers, along with their mood, state of mind, etc. is essential when we look at things from the perspective of preventing human error. |
- |
I think so as well. As far as the differences in awareness among workers go, I believe that this technique makes it possible to evaluate these differences. However, the separation between those evaluating (quality assurance department) and the workers is a problem. Even when the evaluation department requests education and the implementation of countermeasures when evaluation results show differences among the workers, time constraints can lead to situations where it is not possible to provide sufficient education. |
|
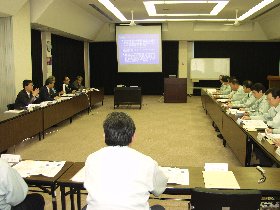
Safety information exchange session |
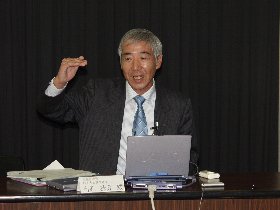
Mr. Takahara |

|
|
|